Flexibilization of combustion plants
Flexibilization of combustion plants
The long-term use of combustion systems requires continuous adaptation to changing fuel properties and operating conditions.
Originally planned assumptions regarding fuel properties and fuel availability can change during operation, as can the required output range. This leads to the previously defined design range of the system being exceeded.
To ensure the flexibility of combustion plants and maximize their efficiency and reliability, we offer two main options: Fuel flexibilization and load range extension. Both approaches are aimed at optimally utilizing your plant and ensuring smooth operation. A key component of this is the EPOC®, which supports you in running your plant stably to its limits, depending on your current requirements.
Would you like to find out more? Should we call you or would you like to receive further information by e-mail?
I am looking forward to answering your questions.
Bernhard Kronberger is your expert concerning process engineering innovations.
Fuel flexibility
The change in fuel properties is much more likely with biogenic and waste fuels than with fossil fuels. The change in both physical and calorific fuel properties can cause problems and have a negative impact on the smooth, trouble-free operation of a combustion plant.
Particular attention must be paid to the change in ash softening temperature, which can lead to caking in the combustion chamber and thus to a reduced travel time.
We offer the following services in the area of fuel flexibilization:
Load range extensions
An expansion of the load range is often the result of a change in the energy user’s requirements. In the area of heat supply, the need to expand the load range often arises due to seasonal fluctuations or network expansion. In summer, for example, the typically reduced heat consumption often requires a reduction in the minimum sustainable load. In addition, new requirements in continuous operation can lead to different load requirements. This means that the firing system must be able to react flexibly to both a minimum load and an increased continuous load.
The task of expanding the load range is related to the task resulting from fuel flexibilization. Extending the design load range of the boiler system involves extensive work to understand and revise the firing system.
The following measures are frequently taken. All measures are of course coordinated with the plant safety concept.
Would you like to find out more? Should we call you or would you like to receive further information by e-mail?
Further information:
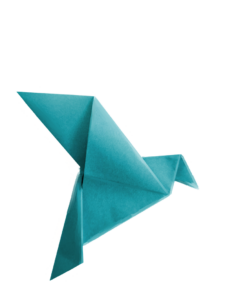
Further information:
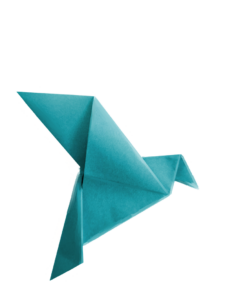