Engineering
At CONENGA Group, we have been leaders in process and control technology plant optimization for many years. We combine several specialist disciplines for the benefit of numerous customers from industry and energy supply in order to make the most of existing plants in terms of comprehensive sustainability – economically, ecologically and technically.
When optimizing and upgrading systems, it is often necessary to adapt existing systems and provide comprehensive services from engineering to implementation. Our experienced team of technologists and engineers is ready to understand your individual requirements and develop customized solutions.
The examples are many and varied: the fuel supply in existing buildings needs to be adapted and automated to make dosing much more precise: We record the inventory, for which there are often no current digital models, in a 3D scan, design the adaptation or redesign, coordinate this technologically and have 3D models at an early stage in order to involve all parties well. Depending on the customer’s wishes, this concept engineering can be followed by handover to the in-house technical department or the adaptation can be continued as a complete package from basic to detailed engineering.
Of course, we accompany the engineering process in the respective level of detail, starting with cost estimates through to suitably precise CAPEX and OPEX calculations, and thus support investment decisions.
I am happy to be there for you!
Dominik Gappmaier is your expert when it comes to engineering and 3D modeling !
The key phases in plant engineering
In plant construction, projects always go through several engineering phases, which are similar regardless of whether it is a new flue gas cleaning system, a conversion of the recirculation air or the retrofitting of a flue gas condensation system.
The fundamentals are outlined in concept or pre-basic engineering, developed in basic engineering and precisely specified in detail engineering.
Concept or Pre-Basic Engineering
In the initial engineering phase, the customer’s requirements and wishes are usually recorded, analyzed and checked for feasibility. Feasibility always involves a combination of technology, systems engineering, cost, requirements and implementation lead time.
The requirement is challenging: decision-makers want to see a clear basis for a decision on the desired solution as a sketch with as little effort as possible, have the effort limited and have a good preview of the effect – quite simply: a basis for a decision.
Basic Engineering
The existing concept from the previous phase now needs to be fleshed out and the loads and dimensions precisely calculated. The main requirements must also be narrowed down further and design specifications must be made for components such as pumps, tanks, heat exchangers, sensors and actuators.
The 3D model visualizes, for example, the embedding, layout and all relevant features of the plant or plant conversion. Costs (CAPEX) and benefits (OPEX, ecology, emissions, etc.) are further specified and risk and safety considerations are integrated in the appropriate depth.
Detail Engineering
The concepts and specifications from basic engineering are reviewed and refined in detail engineering, which is often also carried out by contractors as part of the execution service. The system components are finally dimensioned and detailed. This is where 3D modeling and design play an important role in ensuring precise and efficient planning for all parties involved.
Detail engineering is the solid basis for production and assembly and therefore for implementation.
The “as-built” planning, which is ideally handed over in digital form, should also be seen as an important final part of the detail engineering.
Would you like to find out more? Should we call you or would you like to receive further information by e-mail?
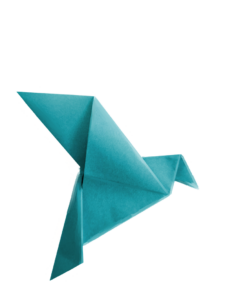