Calcination
Shaping technology for the future together!
Calcination or heating (firing) of minerals containing calcium and magnesium decomposes the carbonate. The resulting products, such as magnesium oxide and carbon dioxide (CO2), play an important role in various industrial processes. These processes are not only crucial for cement and magnesium production, but also for the production of high-quality metal oxides. Our expertise at CONENGA Group helps you to make these processes efficient and sustainable.
Would you like to find out more? Should we call you or would you like to receive further information by e-mail?
I am happy to be there for you!
Bernhard Kronberger is your expert when it comes to calcination!
Calcination
Calcination plays a central role in the production of cement and magnesium. Rotary kilns are mainly used, while special applications such as the production of MgO are often carried out in fluidized bed kilns (e.g. STYROMAG AG, project report).
The main challenge of the process is to reduce the very high primary energy consumption. Our approach to reduction includes burner and combustion chamber optimization as well as support with fuel conversion. Due to the use of substitute fuels, emissions of CO, NOx etc. are also an important aspect andCO2 emissions themselves are a key factor from the operator’s economic point of view.
We see every issue as a specific challenge. We therefore place great importance on developing individual and customized solutions that are sustainable. What unites us is the ability to deal with the complexity and novelty of the challenge in a methodically sound manner and to jointly master the risk inherent in all innovation work in tried and tested work phases with concrete milestones.
Regardless of whether you already have concrete ideas or are still in the idea phase or concept development – we are happy to support you in an initial exchange. We look forward to hearing from you!
Further information:
Calcination
Calcination plays a central role in the production of cement and magnesium. Rotary kilns are mainly used, while special applications such as the production of MgO are often carried out in fluidized bed kilns (e.g. STYROMAG AG, project report).
The main challenge of the process is to reduce the very high primary energy consumption. Our approach to reduction includes burner and combustion chamber optimization as well as support with fuel conversion. Due to the use of substitute fuels, emissions of CO, NOx etc. are also an important aspect andCO2 emissions themselves are a key factor from the operator’s economic point of view.
We see every issue as a specific challenge. We therefore place great importance on developing individual and customized solutions that are sustainable. What unites us is the ability to deal with the complexity and novelty of the challenge in a methodically sound manner and to jointly master the risk inherent in all innovation work in tried and tested work phases with concrete milestones.
Regardless of whether you already have concrete ideas or are still in the idea phase or concept development – we are happy to support you in an initial exchange. We look forward to hearing from you!
Further information:
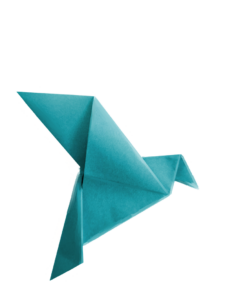